Standards, customer requirements and risks are constantly evolving in the automotive industry. IATF 16949 and TISAX both demand internal process audits to ensure compliance, while some OEMs go further by requiring suppliers to conduct more frequent layered process audits.
In addition, customers today expect zero defects and 100% on-time delivery, and even one quality escape can mean astronomical costs for correction, recalls and lost business.
Automotive suppliers need strong internal process auditing capabilities to meet these demands. The reality for many, however, is that spreadsheets and in-house systems simply aren’t up to the task.
EASE plant floor audit software helps automotive manufacturers tackle these challenges, so they can build streamlined audit programs that deliver substantial reductions in defects, compliance issues and costs.
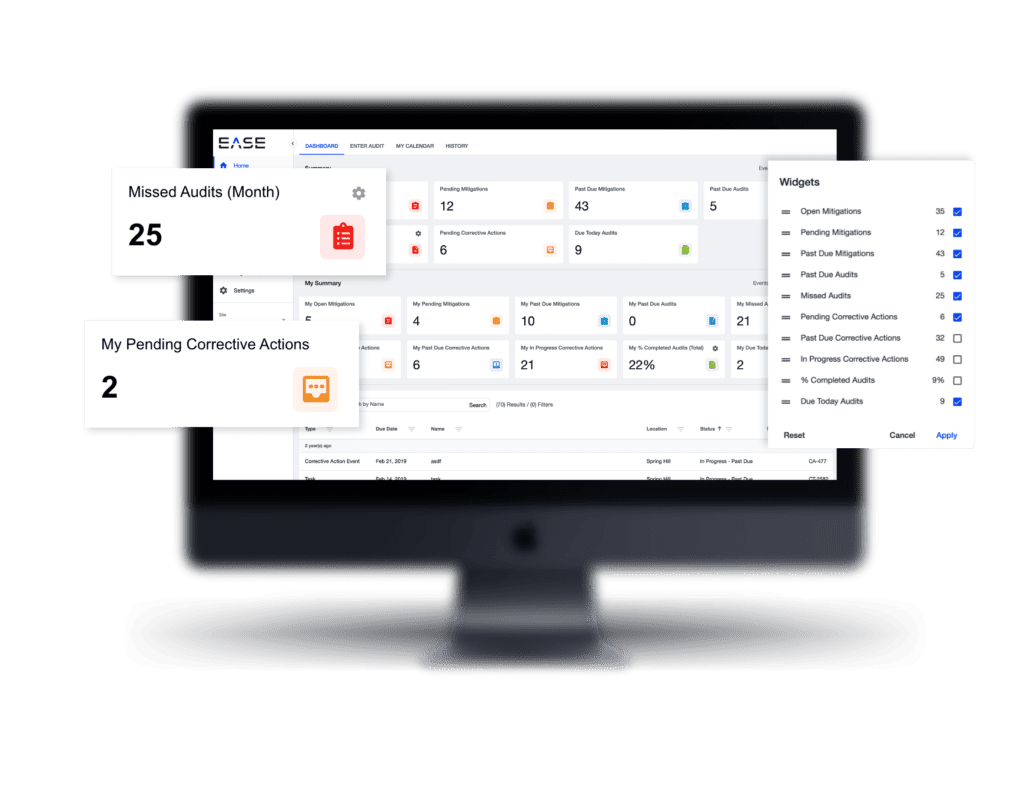
Solving Audit Challenges with EASE
EASE plant floor audit software eliminates many common obstacles of building effective internal audit programs, including:
- Scheduling: Audit administrators can create an entire audit schedule, including layered schedules, with just a few clicks.
- Maintaining updated checklists: Dynamic question libraries make it easy to add, rotate and randomize questions, also supporting multiple question types and follow-up questions.
- Managing different audit types: Plants can create checklists for specific production lines and departments, as well as different audit types such as layered process audits, TISAX and more.
- Conducting audits: E-mail reminders link directly to checklists on a user-friendly mobile app to streamline audits and improve audit completion rates. Photos attached to questions provide clear visual standards, while auditors can also upload photos to support documentation of findings.
- Reporting results and insights: Users can view results immediately, with custom charts and dashboards to spot trends and accelerate root cause analysis.
- Tracking findings and follow-up: Auditors can document on-the-spot corrections and flag items for corrective action to accelerate issue resolutions and minimize quality escapes. New questions can then be added to ensure gains are held in place.
Top automotive suppliers choose EASE because it provides a proven, closed-loop process for proactively identifying, correcting and monitoring process nonconformances. Compared with other audit software, EASE offers more cost-effective pricing based on plant size rather than number of users, with 26 languages supported.
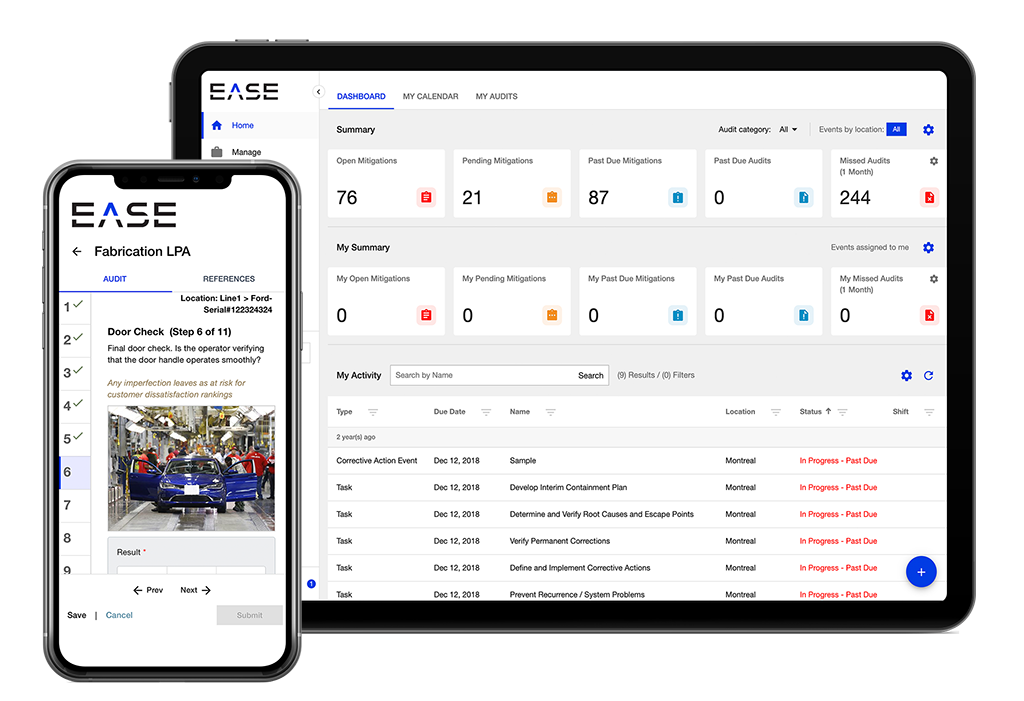
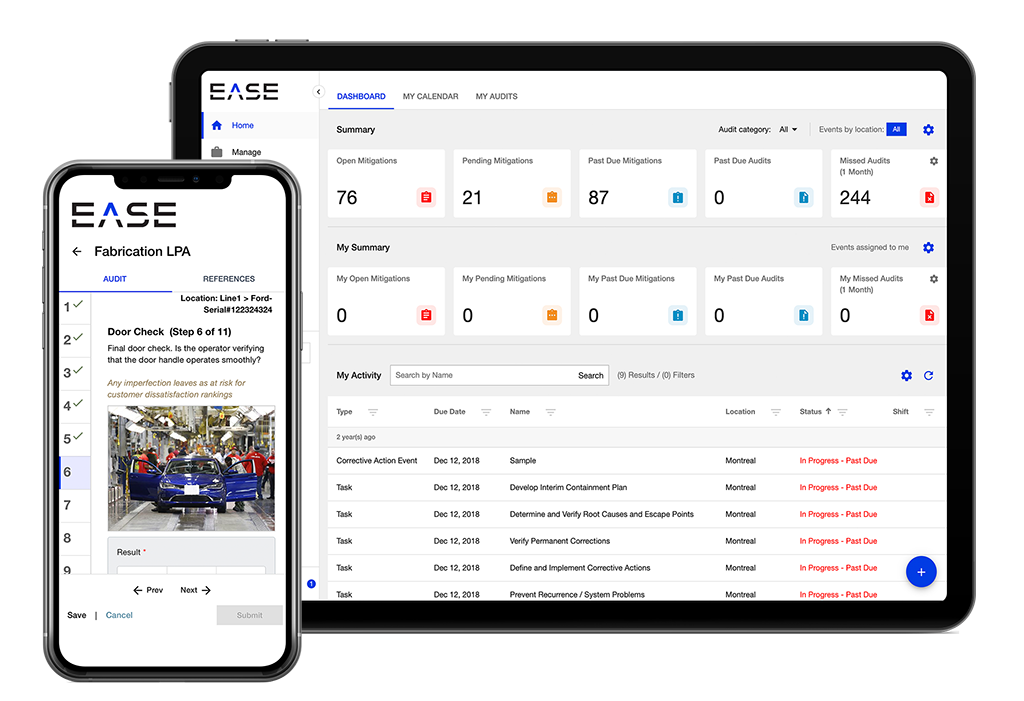
The Choice of Quality Champions
EASE helps manufacturers create a culture of quality where everyone is equipped with the tools and support they need to do their jobs well. Plants receive unmatched support to implement the solution in weeks and start seeing real results faster. Below are just a few examples of what companies have achieved with EASE:
- 50% reduction in quality costs
- 73% reduction in internal PPM
- 53% reduction in customer defects
- 94% fewer overdue corrective actions
Many automotive suppliers also note higher customer satisfaction ratings, as well as fewer external audit findings and higher audit completion rates. With EASE, plants can spend less time managing the details of audit administration, and more time on value-added activities like using audit insights to drive action.
In the fast-paced world of automotive manufacturing, the ability to meet changing requirements while ensuring a high level of quality is paramount. EASE plant floor audit software provides a comprehensive approach to simplifying your audit process, reducing costs and ensuring continuous improvement. From reduced defects and costs to improved relationships with customers, EASE gives suppliers the technology they need to fuel operational excellence and create a culture of quality.
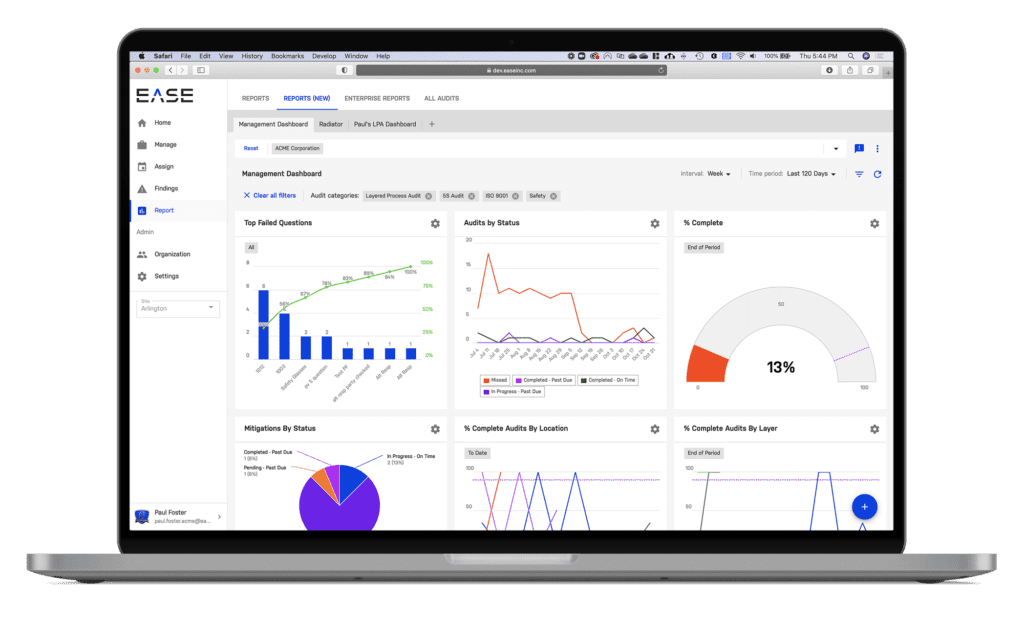
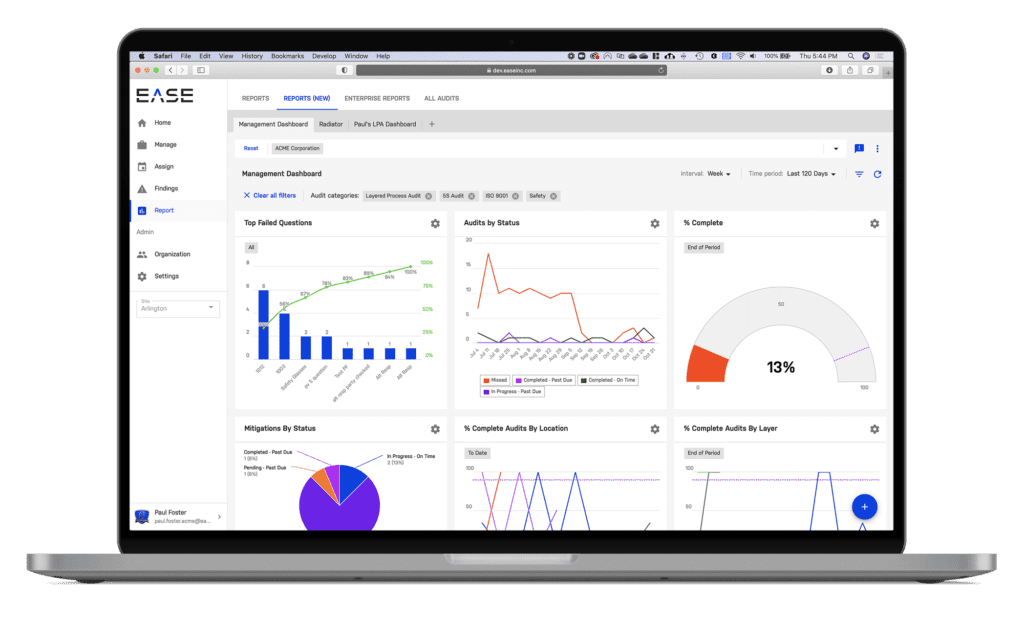
EASE.io – Official sponsor of 12th Regional Automotive Supplier Conference